Frankly it's exhausting, but we gotta do it. We gotta explain how furnaces work! And soon, we'll talk about what will replace them. I'll try to remember to put a link here when that time comes!
Whelp, winter heating season is quickly approaching (in the northern hemisphere anyway) which means that many of us are firing up our heating systems for the first time in many months and hoping for the best.
And how come it seems to work in distinct steps?
What’s a heat exchanger?
Why do we use furnaces at all?
Great questions! So great that I’m making a video to answer them. Now first, we’re gonna be talking about the typical forced-air gas-fired North American heating system in this video because that’s what’s common where I live and what I have access to. Pretty much every small to medium-sized building over here constructed in the last half century or so in a winter climate has at least one of these providing it with heat.
If you’re used to a heating system with a central boiler and radiators, well this isn’t that. Ever since central air conditioning became common, we’ve settled on ducted systems like this where a furnace acts as both the heat source for winter months and air handler for the air conditioner in the summer months. Let’s start by asking what the basic job of the furnace is. You might say, well obviously it’s to provide heat for a living space - and you’d be more-or-less right!
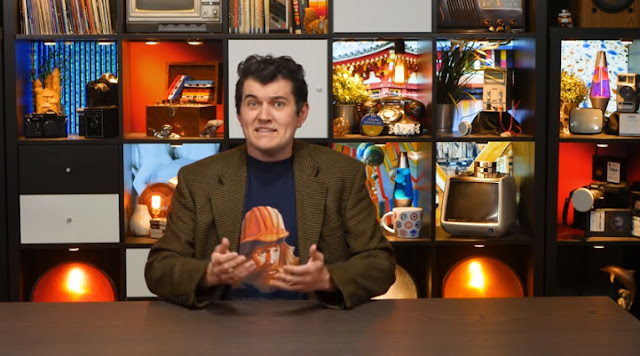
But more specifically, its job is to safely release as much of the heat energy contained in a combustible fuel that it can into the living space and distribute it with the aid of a blower fan and ductwork. Allows itself to run. If it fails its own tests, it locks itself out and you’ll need to call your local HVAC company. Better that than be dead!
We’ll go over that sequence of operations as well as the components themselves shortly but first, let’s discuss why we use these things. If a boiler is what you’re used to, well that makes sense, but quite often I’ve run across folks who seem to think our furnaces are somehow inefficient machines. Not at all, these are incredibly efficient. This particular furnace is able to capture 96% of the heat energy in a fuel. That’s excellent, but some models get even more than that!
So for the rest of this video, if I say “96” I probably meant 95. Anyway, back to the AFUE. It’s measured as a more-or-less yearly average to help account for the differences in efficiency at start-up and shut-down. During a steady heating state it’s actually slightly higher. Being able to get 96% of the heat energy available in a fuel into the living space is tremendous, but even the worst natural gas furnaces on the market have at least an AFUE of 80.
Now, we don’t typically use electric resistive heating to heat entire homes because, while electric heat is itself 100% efficient, electrical generation is not. And even if it were, the electrical requirements of resistive heat aren’t practical on a large scale. But heat pumps are able to turn this math on its head. Since heat pumps, which are basically just air conditioners running in reverse, can move much more energy than they themselves consume, they’re undoubtedly the future of home space heating.
Even right now with our majority fossil-grid, they result in fewer carbon emissions than directly burning fuel because they’re efficiency can approach 500% - more than accounting for the losses in generation. But we’ll save that topic (and its current challenges) for a video in the I Promise not-too-distant future. For now, though, back to this!
Burning pretty much any fuel, including the so-called “clean burning” natural gas produces particulate matter which isn’t great to breathe, and of course there’s the much more immediately deadly combustion by-product carbon monoxide which, through evolutionary bad luck, is much more appealing to your red blood cells than oxygen. Which is bad.
So generally, we shouldn’t burn things indoors. And yet, here’s a device which burns things… indoors. Ah! But this particular furnace is a condensing furnace, and thanks to these two pipes here, the combustion of the fuel sort of happens outside - but more on that later. You may also know of a certain other device which does burn fuel indoors without ventilation - the common stovetop and oven, and research is beginning to suggest that maybe this isn’t so great either.
Anyway, a furnace like this needs to burn its heating fuel and then it has a bit of an exhausting job ahead of itself. Exhausting. The heat exchanger in a standard 80+ furnace is simply some number of typically U-shaped steel tubes. You might call them U-tubes. The fuel is burned inside these tubes, which of course makes them get pretty freaking hot. Those tubes, then, are put in the path of air being forced through the furnace with the aid of a blower motor, and that air keeps the heat exchanger from melting by cooling the tubes down, which also incidentally heats the air. That’s a nice bonus.
The practical upshot of this is that the heat from the fuel gets released into the air flowing through the furnace and eventually out of the vents which heat your home, but the combustion byproducts stay separated inside those tubes.
And also, hang on, you need oxygen to burn fuels and the burning of the fuel consumes that oxygen - so you’re gonna need a way to supply those tubes with fresh air in addition to getting rid of the byproducts. Aha! Well now we’re getting into the more practical and safety bits of the furnace.
If you’ve ever lived with a furnace like this, you’ll likely have noticed that there are two blower motors. But before that one comes on, you hear another one. What’s that for?
Well, that’s arguably the most important part of the furnace. This blower is called the draft inducer, and really it’s more of a sucker. It pulls air - and later, other fun gasses - through the heat exchanger. In other words, it induces a draft.
That air then gets pushed up through some sort of chimney where it will eventually exit the home, or as is the case here it exits through this PVC pipe. And what lives on the other side of those tubes are the flamethrowers. Now we’re getting to the bunny business. If we’re burning a fuel, it’s gotta come from somewhere, and where it comes from is deep underground having been trapped there for millennia before we extracted it. These are essentially just specialized nozzles which release some amount of gas into the heat exchanger’s tubes.
Thanks to the constant supply of fresh air brought about by the draft inducer, it will burn quite nicely.

The draft inducer ensures not only that there is fresh air for burning but also that what comes out the other side of the heat exchanger tubes doesn’t make it into the living space and is instead safely expelled outdoors. Because this device deals with the, frankly, dangerous combination of combustible fuels and enclosed spaces, it’s designed with a number of safety interlocks and a sequence of operations to ensure things don’t go too terribly wrong. But before we get into that, I know this is the second but before we get into that, apologies, let’s discuss the condensing part of this furnace.
A standard 80+ furnace doesn’t really know what to make of that so sends it out with the carbon monoxide and other icky stuff. But that water vapor is hot, and more importantly holds energy in the form of latent heat. When it condenses into a liquid, as it will inevitably do - that’s all the steam you see coming from the rooftops of homes in the dead of winter - it releases that energy. But that’s no good if it’s just happening outside. If we could make it condense inside, we’d be able to get more energy out of the heating fuel. And so, a condensing furnace has what is essentially a second heat exchanger after the main fire tubes with a greater surface area that can cool the exhaust gases.
That’s how this furnace is able to get 96% of the energy available in the fuel into the home. I mean, think about this, it’s burning flammable gas, there’s literal fire inside of it, and it outputs 70,000 BTUS or about 20 kilowatts of heat. And yet, it loses so little of that heat in the exhaust that it can safely exit through a plastic pipe which barely gets warm at all.
Compare that to an 80+ furnace with a steel exhaust chimney that gets so hot you can’t even touch it, and you’ll understand why condensing furnaces are a big deal and a great idea. A condensing furnace is a little more complicated, of course, than a conventional one. Most of that has to do with the fact that dealing with the condensate isn’t the easiest task for one, well now you have to deal with it when previously you didn’t. This furnace has a drain pipe on its side for that very reason.
But also that water isn’t just plain water, it’s pretty acidic thanks to other combustion byproducts so the secondary heat exchanger needs to be made of materials, such as stainless steel, which resist corrosion. This adds somewhat to the cost of the furnace, but getting an extra 10 or 15% of the energy out of your heating fuel makes it, to my mind, obviously worth it and we absolutely should find ways to help subsidize the added cost for those who need financial assistance because in the long run it will always save money and resources.
It’s frankly a no-brainer at this point. Oh, and that other pipe there? Well, here’s another way to get an increase in efficiency. This furnace gets its oxygen supply from outside. This pipe is simply supplying the combustion section with outside air, in fact you can see that it just opens to this space (and the other end is outside). Why do that?
Well, a conventional furnace gets its combustion air from the room it’s sitting in. That means it creates negative pressure whenever the draft inducer is running, and that brings in some amount of cold outside air to replace what leaves through the exhaust. In contrast, this supply pipe, along with the seals in this panel, makes it so that the combustion section of the furnace is essentially entirely outdoors, creating no negative pressure at all. Of course, particularly right now in the human experience we’re discovering that we really ought to have a little more exchange of air than we do.
But anyway, Let’s finally bring it back to the start with one of the questions I asked; why does the furnace seem to do things in distinct steps? Ah, well that’s all about that safety. There really aren’t that many components in a basic household furnace: just the draft inducer, heat exchanger, main blower, an igniter, and a gas valve. And to do that, we rely on a few sensors and a sequence of operations. Since this furnace is quite modern we have a circuit board with a microprocessor handling everything, but the same basic things have been happening in forced-air furnaces for decades.
When the thermostat calls for heat, the sequence of operations begins by turning on the draft inducer. Now, this component absolutely must be functioning properly for the safe operation of the furnace. If it opened the gas valve without airflow through the heat exchanger, it could be a disaster.
So, to prove that the inducer is actually functional, the circuit board looks for the output from this pressure switch to change. If it did, that means there was a change in air pressure where the switch is located, which would only occur if the draft inducer is working. Looking for a change in switch output also allows the furnace’s logic board to detect a stuck switch and refuse to operate. Once the operation of the draft inducer has been proven, there will be a pre-programmed delay period to ensure no unburnt gasses remain in the heat exchanger.
Assuming the furnace shut down correctly there shouldn’t be any, but better safe than sorry. While that delay is happening, this furnace sends power to the hot surface igniter. This is an igniter that ignites the fuel by being a surface which is hot. Anyway, because it takes a while for the hot surface igniter to become hot enough that its surface can ignite things, the delay period for clearing the heat exchanger is a perfect time to warm it up. Next comes the opening of the gas valve. This is a very time-sensitive step because natural gas and propane, which is actually what fuels this furnace - I’m really in the middle of nowhere...can be explosive!

And this is actually really easy to do, we just use a thermocouple as a flame sensor to detect a rapid rise in heat brought about by flames. And this is done quite cleverly. The hot surface igniter lives here next to the rightmost burner. And so, to determine that ignition happened correctly, the flame sensor is placed at the burner that’s farthest away from the igniter.
It will thus only register a flame when all burners have successfully ignited. When the furnace opens the gas valve, it looks for a rapid rise in temperature from that sensor and it should see it right away. If it doesn’t, usually within just two seconds, it closes the gas valve and aborts its mission.
If that’s allowed to happen for more than just a couple of seconds, a dangerous quantity of fuel may now exist in the heat exchanger which, if it were to ignite, would be likely to damage it. And that’s very bad and also dangerous.
And after a certain number of failed attempts - it’s five in the case of this furnace - the system locks itself out and no heat for you. So it does self-reset to keep your pipes from freezing if it can help it. So long as the flame sensor sensed flames, though, the logic board then gives the all-clear for the next step. Which is to wait a lilt’ bit. Rather than start the blower motor right away and give you a nice blast of cold air, the furnace will simply sit pretty and allow the heat exchanger to get a little hot before it switches on the blower. But once it does that, well now you’ve got heat coming from your heat vents.
When the thermostat is satisfied and it stops calling for heat, the gas valve closes, extinguishing the flames, and the inducer fan remains running for thirty seconds or so to make sure all the remaining exhaust is replaced by fresh air. At the same time, the blower motor keeps running to cool off the heat exchanger and, of course, get the rest of the heat it contains out of it. But after about a minute, it shuts down completely and patiently waits for the next call for heat.
Now there’s gonna be at least one other safety device in the furnace, too, and that would be a limit switch. This is a switch which trips at a certain temperature, and it’s designed to protect against overheating. If for some reason the blower motor stopped working, or airflow was restricted in some other way, the heat exchanger will overheat before too long because it doesn’t have enough airflow to cool itself down. So, that limit switch is there to detect such a scenario and shut down the furnace if it occurs.
So, there’s clearly a lot of safety built into your typical furnace, and some clever ingenuity, too. But there’s one thing it generally won’t guard you from, and that’s carbon monoxide poisoning. If everything is in working order, that shouldn’t be possible, but…well whenever you burn fuel there’s a risk of carbon monoxide.
Furnaces can be particularly tricky because the heat exchanger wears out with time. Going from room temperature to having fire inside of it and back a dozen times per day for 15 years is hard on it, and over time imperfections can form from this thermal stress. The most dangerous kind is a crack in the heat exchanger’s tubes, which can allow exhaust gasses - and thus carbon monoxide to exit the heat exchanger and make it into the living space.
Comments
Post a Comment